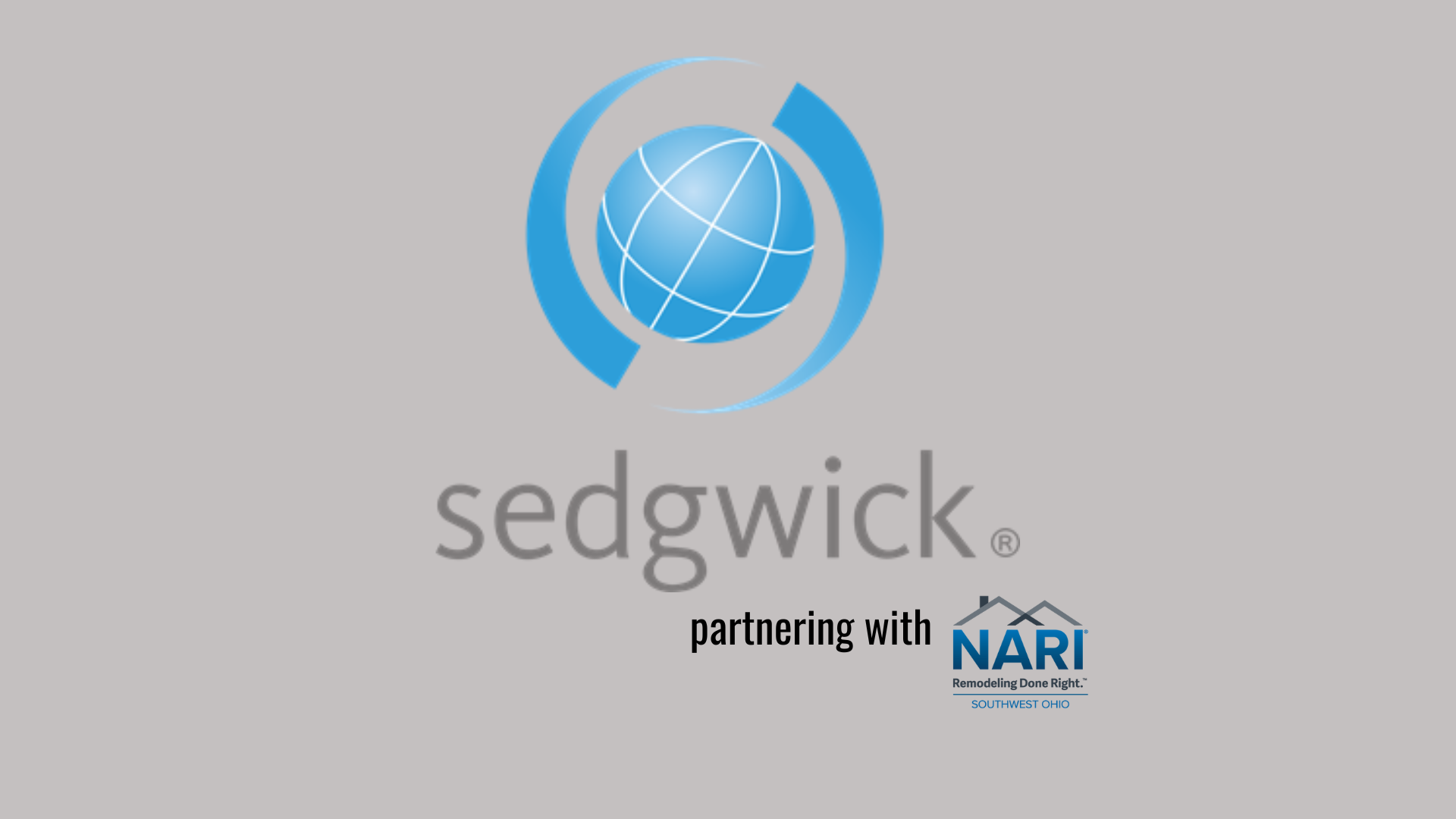
Forklift Safety in the Workplace
Forklifts, also known as powered industrial trucks, play a crucial role in various industries, from manufacturing and construction to warehousin and logistics. However, if not managed properly, their operations pose significant risks to both operators and bystanders. Implementing comprehensive safety measures and adhering to regulations is paramount to prevent accidents and ensure a secure working environment.
Between 2021 and 2023, there were approximately 198 fatalities that resulted from forklift operation. Recent data identifies the causes of forklift fatalities by type of accident:
Type of Accident / Percentage
Crushed by tipping vehicle - 42%
Crushed between vehicle and a surface - 25%
Crushed between two vehicles - 11%
Struck or run over by vehicle - 10%
Struck by falling material - 8%
Fall from platform on forks - 4%
Accidental activation of controls - 2%
The Occupational Safety and Health Administration’s (OSHA) standard 29 CFR 1910.178 spells out the requirements for safe operation of forklifts. Some of the highlight of the standard include:
Pre-Shift Inspections
Employers are required to perform a pre-shift examination of the forklift. Under OSHA’s regulation 29 CFR 1910.178(q)(7), “Industrial trucks shall be examined before being placed in service, and shall not be placed in service if the examination shows any condition adversely affecting the safety of the vehicle. Such examination shall be made at least daily.” The regulation goes on to say “Where industrial trucks are used on a round-the-clock basis, they shall be examined after each shift. Defects when found shall be immediately reported and corrected.” If, during examination, a deficiency is found and the forklift cannot be operated safely, it must be taken out of service. Whether you use the manufacturers recommendation or create your own checklist be sure to document each inspection. It is important to have a process to remove the key and prevent employees from operating the forklift until it is safe to do so.
Employee Training
Per OSHA, around 20-25% of forklift-related injuries are caused by inadequate training. Safe operation and training requirements can be found under 29 CFR 1910.178 (l). Highlights of employee training include:
• Safe Operation
o Employers shall ensure that each operator is competent to operate a forklift, as demonstrated by successful completion of the training.
o No employee shall operate a forklift (except for training purposes) until they have successfully completed all required training.
• Training Program Implementation
o Training shall consist of formal instructions, practical training and evaluation of the operator’s performance in the workplace.
o Training and evaluation must be done by a person with knowledge, training and experience to train operators and evaluate their competence.
o Trainees may operate forklifts only under the direct supervision of a person who has the knowledge, training and experience to train operators.
o Training may be performed as long as it does not endanger the trainee or other employees.
• Training Program Content - Initial training requires employees to understand the limitations of the forklift. Some of these limitations include:
o Engine or motor operations and operating instructions.
o Warnings and precautions, steering and maneuverability.
o Visibility, stability, vehicle inspection and maintenance.
o Differences between the truck and an automobile.
• Refresher Training and Evaluation - As with any safety program, retraining employees is key to safe operation. Highlights of refresher training include:
o Evaluation of competency tests for employees every three years.
o Retraining is required if:
▪ The operator is involved in an accident or near miss.
▪ The operator is observed operating the forklift in an unsafe manner.
▪ The operator receives an unsatisfactory evaluation.
▪ The operator is assigned to a different type of truck.
▪ If there are changes in the workplace in a manner that could affect the safe operation of the forklift.
• Avoidance of Duplicative Training
o If an operator has previously received training and such training is appropriate to the truck and
working conditions encountered, additional training in that topic is not required if the operator
is found competent and has been evaluated to operate the truck safely.
• Certification
o Employees must be trained and evaluated and the certification must have the name of the operator, the date of training, and the name of the person(s) performing the training or evaluation.
Powered Industrial Vehicles offer a variety of services that can make our jobs easier, but they need to be respected. Inspections, operations, maintenance and communication are key to keeping the workplace safe and protecting employees. Following the above guidelines and other requirements within the standard will help in developing a policy on proper forklift operation and training of employees. Otherwise, you are putting your employees at risk for a potential injury, fatality or an OSHA citation.
OSHA’s full Powered Industrial Trucks regulation can be found at (https://www.osha.gov/laws-regs/regulations/standardnumber/1910/1910.178).
For more information on OSHA's Local Emphasis Program on Powered Industrial Trucks, go to https://www.osha.gov/sites/default/files/enforcement/directives/cpl-04-05-2305.pdf.
If you need help identifying potential hazards in your workplace, please contact Andy Sawan, risk services specialist at Sedgwick at andrew.sawan@sedgwick.com or (330) 819-4728.
For more information on OSHA’s Local Emphasis Program on Powered Industrial Trucks, go to
https://www.osha.gov/sites/default/files/enforcement/directives/cpl-04-05-2305.pdf.
If you need help identifying potential hazards in your workplace, please contact Andy Sawan, risk
services specialist
at Sedgwick at andrew.sawan@sedgwick.com or 330.819.4728.