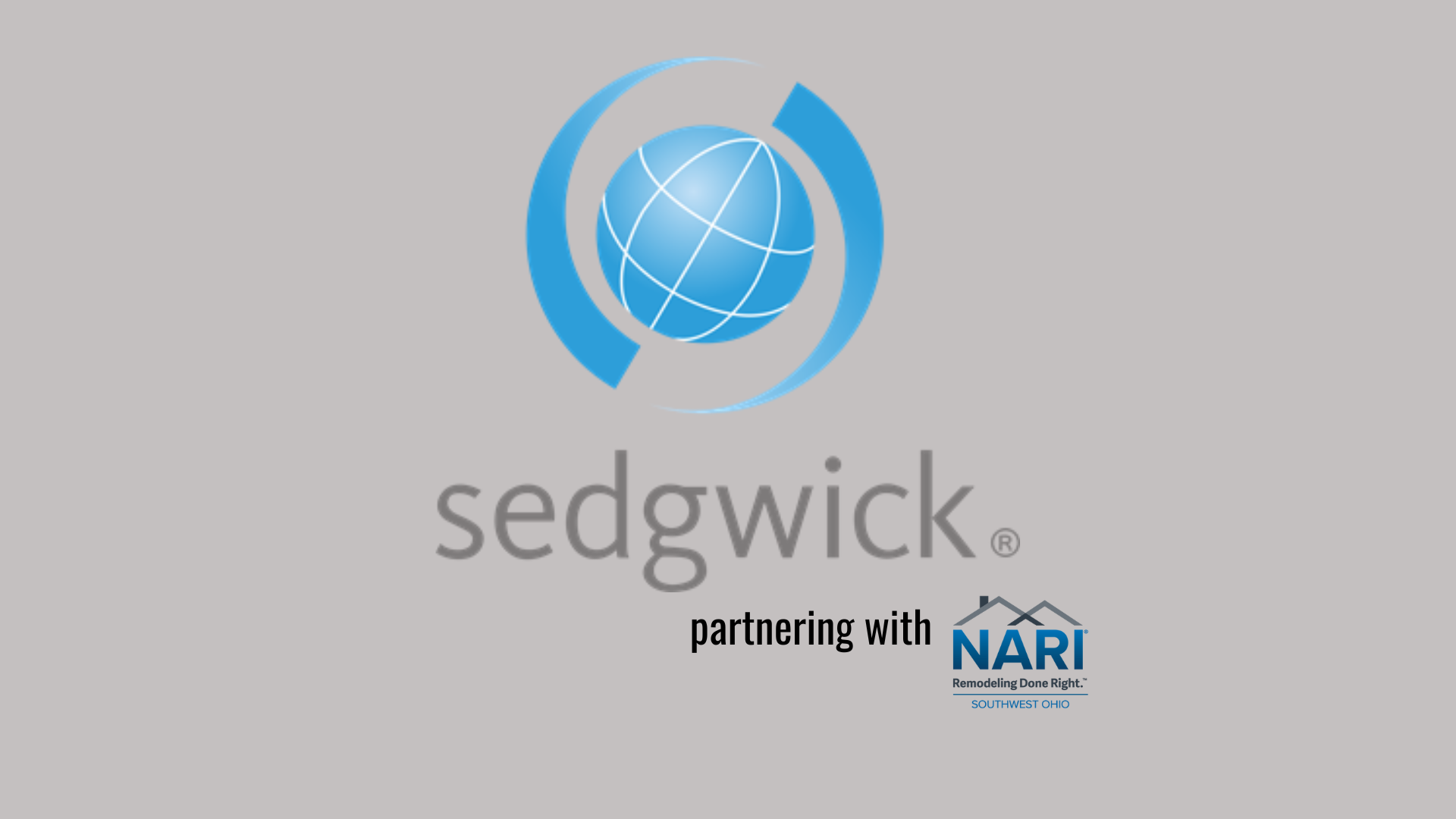
Safeguarding Machinery
Various types of machines pose hazards to employees that can result in injuries that include crushing, entrapment, amputations, and even death. These hazardous areas, known as danger zones, are machine parts that must be guarded to protect employees from injury. The Occupational Safety and Health Administration (OSHA) defines a danger zone as “any place in or about a machine or piece of equipment where an employee may be struck by or caught between moving parts, caught between moving and stationary objects or parts of the machine, caught between the material and a moving part of the machine, burned by hot surfaces or exposed to electric shock.”
Per OSHA’s General Requirements for Machine Guarding (29 CFR 1910.212), employers are required to perform an evaluation of the machinery in their workplace in order to identify and adequately guard the danger zones to provide protection to employees. In fact, machine guarding violations frequently show up as one of the OSHA’s top ten most cited violations each year. So not only is it essential to protect employees, but an effective machine guarding program will help in the event of an OSHA Inspection.
It is essential first to understand the movements of machinery to identify the danger zones. There are two types of hazardous movements that a machine makes: Mechanical Motions and Mechanical Actions.
Mechanical Motions – Mechanical motions include gears, pulleys, or moving belts. There are basically four different types of mechanical motions.
Rotating – Rotating motions include collars, couplings, cams, flywheels, shaft ends, spindles, and horizontal or vertical shafts. These are dangerous as they may grip hair, clothing, and body parts. Additional dangers on rotating parts include when projections exist, such as set screws, bolts, nicks, and abrasions.
In-running Nip Points – These hazards are caused by rolling parts on machinery. The basic types of in-running nip points include parts that rotate in opposite directions, such as rolling mills and calenders, and rotating and fixed parts that create a shearing, crushing, or abrading action. In addition, rotating parts between power transmission belts and pulleys, a chain and sprocket, and a rack and pinion.
Reciprocating – Reciprocating is an action caused by a back-and-forth motion where a worker may get struck by or caught between a moving and stationary part.
Transversing – This movement is a straight, continuous line, such as the motion of a belt to moving parts.
Mechanical Actions – These actions are defined as where the work is being performed. There are four types of mechanical actions.
Cutting – The cutting action involves rotating, reciprocating and transverse motions. Types of these actions include bandsaws, circular saws, boring and drilling machines, lathes and milling machines.
Punching – Punching action refers to power when applied to the ram (slide). Work examples of punching include stamping of metal or other materials.
Shearing – The shearing action refers to applying power to slide a knife to trim or shear material. Shearing machines can be powered mechanically, hydraulically, or pneumatically.
Bending – The bending action refers to power applied to a slide or ram to draw or stamp metal or other materials. Types of equipment that bend materials include power presses and press brakes.
Once you understand the different types of danger zones, perform an audit of your facility. Keep an open mind and check every department with machinery, regardless of the equipment size. Once you’ve identified the machinery, check to see if the guarding meets OSHA’s General Requirements for Machine Guarding (29 CFR 0.212). If not, you will need to upgrade to meet those requirements.
There are different types of guards, but they typically fall under two categories:
Barrier Guards – This can involve physical barriers, such as fences, screens, or shields, to prevent access to the danger zone. Barrier guards should be designed to prevent contact with moving parts while allowing the machine to function effectively. The basic types of guards include:
a. Fixed
b. Interlocked
c. Adjustable
d. Self-adjusting
Interlocks and Safety Device Guards – Use interlocks and safety devices to ensure that machinery cannot operate unless all guards are in place and secure. These devices can include safety switches, sensors, and emergency stop buttons. Types of interlock and safety device guards
include:
a. Photoelectric
b. Radiofrequency
c. Electro-Mechanical
d. Pull Back and Restraints
e. Safety Trip Controls
f. Two-Hand Control or Two-Hand Trip
g. Gate
Once you’ve installed the barrier guard or interlocks/safety device guard, train employees, schedule regular maintenance and develop any needed Lockout Tagout procedures. This is a great way to communicate the purpose of the guard to employees. It would be best to place warning signs or labels to identify the danger zone clearly. These warnings should be easily visible and understood by all employees.
Properly guarding the danger zone is a critical aspect of workplace safety, and employers should prioritize it to protect their employees and comply with safety regulations. Additionally, continuous monitoring and improvement of safety procedures are essential to adapt to changing circumstances and prevent accidents.
If you have further questions regarding machine guarding or would like more information, please contact Andy Sawan at Sedgwick at andrew.sawan@sedgwick.com or 330-819-4728.